Definição de usinabilidade
É o grau de dificuldade de se usinar um determinado material / processo
As propriedades do material que podem afetar na usinabilidade são:
Dureza
Resistência a tração
Ductilidade
Condutividade térmica
Taxa de encruamento
Ferros fundidos são ligas ferro-carbono com porcentagem de carbono entre 2 e 4%, contendo ainda outros elementos de liga como o silício, o manganês, o fósforo e o enxofre, além do níquel, cromo, molibdênio e cobre.
O ferro fundido cinzento forma cavacos de ruptura, enquanto que os maleáveis e nodulares formam cavacos longos.
A influência dos elementos pode ser dividida em 2 tipos:
Os formadores de carboneto (cromo, cobalto, manganês, molibdênio e vanádio) que prejudicam a usinabilidade devido ao fato de que os carbonetos são partículas muito duras e abrasivas.
Os grafitizantes (silício, níquel, alumínio e cobre) auxiliam na usinabilidade.
O sulfeto de manganês também é utilizado nos ferros fundidos para melhorar a usinabilidade.
Em termos gerais podemos dizer que quanto maior a dureza e a resistência de um tipo de ferro fundido pior é a sua usinabilidade.
Propriedades mecânicas
Aumento da Dureza / Resistência a tração
Dificulta a usinabilidade
Aumenta os esforços de corte
Aumento da Ductilidade
Melhora a usinabilidade
Favorece a formação dos cavacos
Diminui os esforços de corte
Tendências a formação de aresta postiça
Aumento da Condutividade térmica
Melhora a usinabilidade
Diminui o calor gerado na região de corte
Aumento da Taxa de encruamento
Dificulta a usinagem
Dificulta a formação de cavacos
Aumenta os esforços de corte
Tendências a formação de aresta postiça
quarta-feira, 9 de dezembro de 2009
OUTROS MATERIAIS PARA PASTILHAS INTERCAMBIÁVEIS
Materiais Cerâmicos
Cerâmica Pura (Branca): Á base de óxido alumínio.
Aplicações: Acabamento de Aço e Ferro Fundido.
Cerâmica Mista (Cinza): É composta de alumina, carboneto de titânio e nitreto de titânio.
Aplicação: Torneamento em Aço Endurecido e Ferro Fundido.
Cermets: É composta de materiais metálicos e cerâmicos
Aplicação: Acabamento aço de dureza 34 a 66 HRc e ferro fundido com dureza superior a 235 HB.
Cuidados com Cerâmica: Chanfro na aresta, chanfro na peça, espessura da pastilha, geometria negativa e fixação com grampo.
Nitreto Cúbico de Boro (CBN / PCBN):
É um material sintético obtido pela reação química, possuindo uma estrutura de grafite.
Dureza: 4000 HV ~ (240 HRc).
Aplicações: Na usinagem de aços duros ( de 45 a 65 HRc ) e ferro fundido, tanto no fresamento como no torneamento.
Materiais com cavacos curtos.
CBN para desbaste (ap = 0,5 a 0,8 mm ).
CBN para acabamento (ap menor que 0,5 mm ).
Cuidados com CBN: Sistema de fixação o mais rígido possível, chanfro na aresta de corte e fluido de corte sempre que possível.
Diamante Artificial (PCD):
PCD é um material sinterizado a uma temperatura de 1400 ºC a 2000ºC.
Vantagens:
Altíssima dureza 7.500 HV ~(450 HRc).
Alta tenacidade.
Alta condutividade térmica.
Desvantagens:
Baixa estabilidade química.
Aplicações: Usinagem de materiais não ferrosos.
Cerâmica Pura (Branca): Á base de óxido alumínio.
Aplicações: Acabamento de Aço e Ferro Fundido.
Cerâmica Mista (Cinza): É composta de alumina, carboneto de titânio e nitreto de titânio.
Aplicação: Torneamento em Aço Endurecido e Ferro Fundido.
Cermets: É composta de materiais metálicos e cerâmicos
Aplicação: Acabamento aço de dureza 34 a 66 HRc e ferro fundido com dureza superior a 235 HB.
Cuidados com Cerâmica: Chanfro na aresta, chanfro na peça, espessura da pastilha, geometria negativa e fixação com grampo.
Nitreto Cúbico de Boro (CBN / PCBN):
É um material sintético obtido pela reação química, possuindo uma estrutura de grafite.
Dureza: 4000 HV ~ (240 HRc).
Aplicações: Na usinagem de aços duros ( de 45 a 65 HRc ) e ferro fundido, tanto no fresamento como no torneamento.
Materiais com cavacos curtos.
CBN para desbaste (ap = 0,5 a 0,8 mm ).
CBN para acabamento (ap menor que 0,5 mm ).
Cuidados com CBN: Sistema de fixação o mais rígido possível, chanfro na aresta de corte e fluido de corte sempre que possível.
Diamante Artificial (PCD):
PCD é um material sinterizado a uma temperatura de 1400 ºC a 2000ºC.
Vantagens:
Altíssima dureza 7.500 HV ~(450 HRc).
Alta tenacidade.
Alta condutividade térmica.
Desvantagens:
Baixa estabilidade química.
Aplicações: Usinagem de materiais não ferrosos.
terça-feira, 8 de dezembro de 2009
AÇOS FERRAMENTAS
Definição
Os aços-ferramentas são aqueles utilizados nas operações de corte, formação, afiação e quaisquer outras relacionadas com a modificação de um material para um formato utilizável. Estes aços se caracterizam pelas suas elevadas dureza e resistência à abrasão geralmente associadas à boa tenacidade e manutenção das propriedades de resistência mecânica em elevadas temperaturas.
Estas características normalmente são obtidas com a adição de elevados teores de carbono e ligas, como tungstênio, molibdênio, vanádio, manganês e cromo. Boa parte dos aços-ferramenta são forjados, mas alguns também são fabricados por fundição de precisão ou por metalurgia do pó. A seleção da matéria-prima para a fabricação dos aços ferramentas é um fator importante do processo, e a sua seleção costuma ser cuidadosamente realizada inclusive na utilização de sucata.
A fusão dos aços-ferramentas é realizada, normalmente, em quantidades relativamente pequenas nos fornos elétricos, tomando-se um especial cuidado com as tolerâncias de composição química e homogeneidade do produto final. Estas e outras particularidades tornam o aço-ferramenta um material de custo mais elevado do que os aços comuns.
Classificação
Devido às diversas utilizações dos aços-ferramentas, eles são divididos em diferentes tipos de acordo com a sua aplicação e características. São eles:
· Aços-rápido: são desenvolvidos para aplicações de usinagem em elevadas velocidades. Existem duas classificações para os aços-rápidos, que são os ao molibdênio (grupo M) e os ao tungstênio (grupo T). Os dois possuem uma performance mais ou menos semelhante. Os do grupo M, entretanto, tem um custo inicial menor.
· Aços para trabalho a quente: desenvolvidos para utilização em operações de punçonamento, cisalhamento e forjamento de metais em altas temperaturas sob condições de calor, pressão e abrasão. São identificados como aço H, no sistema de classificação. São divididos em três sub-grupos: ao cromo (que vai do H10 ao H19) , ao tungstênio (H21 ao H26) e ao molibdênio (H42 e H43).
· Aços para deformação a frio: por não conter os elementos de liga necessários para possuir resistência a quente, estes aços se restringem a aplicações que não envolvam aquecimentos repetidos ou prolongados em faixas de temperatura de 205 a 260ºC. São divididos em três grupos: aços temperáveis ao ar (grupo A), alto-carbono e alto-cromo (grupo D) e temperáveis em óleo (grupo O)
· Aços resistentes ao choque: seus principais elementos de liga são manganês, silício, cromo, tungstênio e molibdênio Quase todos os aços deste tipo (conhecidos como Grupo S) possuem conteúdo de carbono de aproximadamente 0.50%, o que lhes confere uma combinação de elevadas resistência e tenacidade e baixa ou média resistência ao desgaste por abrasão.
· Aços baixa-liga para aplicações especiais: contém pequenas quantidades de cromo, vanádio, níquel e molibdênio. A demanda por estes aços vem caindo continuamente, o que reduziu os seus subgrupos de sete para apenas dois, ambos temperáveis a óleo. São os aços do grupo L.
· Aços para moldagem: estes aços possuem cromo e níquel como principais elementos de liga. Possuem características de baixa resistência ao amolecimento em altas temperaturas. São utilizados quase que exclusivamente em peças fundidas sob pressão ou em moldes para injeção ou compressão de plásticos e são classificados como grupo P.
· Aços temperáveis em água: nestes aços o carbono é o principal elemento de liga. São adicionados, também, pequenas quantidades de cromo para aumentar a temperabilidade e a resistência à abrasão, e de vanádio, para manter uma granulação fina, e conseqüentemente uma maior tenacidade. Pertencem ao grupo W.
Aplicações
· Aços-rápido: ferramentas, brocas, perfuratrizes, alargadores de furos, machos para abertura de roscas e fresas helicoidais. Alguns graus podem ser utilizados para certas aplicações a frio como laminadores de rosca, punções e matrizes para corte de discos.
· Aços para trabalho a quente: os aços ao cromo são utilizados em aplicações de transformações mecânicas a temperaturas elevadas. Os aços ao tungstênio são utilizados como mandris ou matrizes de extrusão para aplicações de alta temperatura, como por exemplo, na extrusão de ligas de cobre, ligas de níquel e aço.
· Aços para deformação a frio: os do grupo A são aplicados como facas de cisalhamento, punções, corte de chapas para estampagem e matrizes para aparar. Os do grupo D são aplicados em ferramentas de forjamento, rolos de laminação de roscas, estampagem profunda, moldes de tijolo, calibres, operações de brunimento, rolos e facas para corte de tiras. Os do grupo O, por fim, são utilizados em matrizes e punções para corte de chapas para estampagem, rebarbação, trefilação, flangeamento e forjamento.
· Aços resistentes ao choque: usados em talhadeiras, formões, contra-rebites, punções, brocas-guia e outras aplicações que requerem elevada tenacidade e resistência ao choque.
· Aços baixa-liga para aplicações especiais: são utilizados, de um modo geral, em componentes de máquinas como árvores, cames, placas, mandris e pinças de tornos
· Aços para moldagem: como o próprio nome sugere, estes aços são utilizados como moldes de vários tipos, para aplicações que requerem a manutenção das características de resistência em temperaturas e pressões elevadas.
· Aços temperáveis em água: são utilizados em ferramentas para forjamento a frio, cunhagem de moedas, gravação em relevo, trabalho em madeira, corte de metais duros (machos e alargadores), cutelaria e outras que requeiram resistência ao desgaste por abrasão.
Os aços-ferramentas são aqueles utilizados nas operações de corte, formação, afiação e quaisquer outras relacionadas com a modificação de um material para um formato utilizável. Estes aços se caracterizam pelas suas elevadas dureza e resistência à abrasão geralmente associadas à boa tenacidade e manutenção das propriedades de resistência mecânica em elevadas temperaturas.
Estas características normalmente são obtidas com a adição de elevados teores de carbono e ligas, como tungstênio, molibdênio, vanádio, manganês e cromo. Boa parte dos aços-ferramenta são forjados, mas alguns também são fabricados por fundição de precisão ou por metalurgia do pó. A seleção da matéria-prima para a fabricação dos aços ferramentas é um fator importante do processo, e a sua seleção costuma ser cuidadosamente realizada inclusive na utilização de sucata.
A fusão dos aços-ferramentas é realizada, normalmente, em quantidades relativamente pequenas nos fornos elétricos, tomando-se um especial cuidado com as tolerâncias de composição química e homogeneidade do produto final. Estas e outras particularidades tornam o aço-ferramenta um material de custo mais elevado do que os aços comuns.
Classificação
Devido às diversas utilizações dos aços-ferramentas, eles são divididos em diferentes tipos de acordo com a sua aplicação e características. São eles:
· Aços-rápido: são desenvolvidos para aplicações de usinagem em elevadas velocidades. Existem duas classificações para os aços-rápidos, que são os ao molibdênio (grupo M) e os ao tungstênio (grupo T). Os dois possuem uma performance mais ou menos semelhante. Os do grupo M, entretanto, tem um custo inicial menor.
· Aços para trabalho a quente: desenvolvidos para utilização em operações de punçonamento, cisalhamento e forjamento de metais em altas temperaturas sob condições de calor, pressão e abrasão. São identificados como aço H, no sistema de classificação. São divididos em três sub-grupos: ao cromo (que vai do H10 ao H19) , ao tungstênio (H21 ao H26) e ao molibdênio (H42 e H43).
· Aços para deformação a frio: por não conter os elementos de liga necessários para possuir resistência a quente, estes aços se restringem a aplicações que não envolvam aquecimentos repetidos ou prolongados em faixas de temperatura de 205 a 260ºC. São divididos em três grupos: aços temperáveis ao ar (grupo A), alto-carbono e alto-cromo (grupo D) e temperáveis em óleo (grupo O)
· Aços resistentes ao choque: seus principais elementos de liga são manganês, silício, cromo, tungstênio e molibdênio Quase todos os aços deste tipo (conhecidos como Grupo S) possuem conteúdo de carbono de aproximadamente 0.50%, o que lhes confere uma combinação de elevadas resistência e tenacidade e baixa ou média resistência ao desgaste por abrasão.
· Aços baixa-liga para aplicações especiais: contém pequenas quantidades de cromo, vanádio, níquel e molibdênio. A demanda por estes aços vem caindo continuamente, o que reduziu os seus subgrupos de sete para apenas dois, ambos temperáveis a óleo. São os aços do grupo L.
· Aços para moldagem: estes aços possuem cromo e níquel como principais elementos de liga. Possuem características de baixa resistência ao amolecimento em altas temperaturas. São utilizados quase que exclusivamente em peças fundidas sob pressão ou em moldes para injeção ou compressão de plásticos e são classificados como grupo P.
· Aços temperáveis em água: nestes aços o carbono é o principal elemento de liga. São adicionados, também, pequenas quantidades de cromo para aumentar a temperabilidade e a resistência à abrasão, e de vanádio, para manter uma granulação fina, e conseqüentemente uma maior tenacidade. Pertencem ao grupo W.
Aplicações
· Aços-rápido: ferramentas, brocas, perfuratrizes, alargadores de furos, machos para abertura de roscas e fresas helicoidais. Alguns graus podem ser utilizados para certas aplicações a frio como laminadores de rosca, punções e matrizes para corte de discos.
· Aços para trabalho a quente: os aços ao cromo são utilizados em aplicações de transformações mecânicas a temperaturas elevadas. Os aços ao tungstênio são utilizados como mandris ou matrizes de extrusão para aplicações de alta temperatura, como por exemplo, na extrusão de ligas de cobre, ligas de níquel e aço.
· Aços para deformação a frio: os do grupo A são aplicados como facas de cisalhamento, punções, corte de chapas para estampagem e matrizes para aparar. Os do grupo D são aplicados em ferramentas de forjamento, rolos de laminação de roscas, estampagem profunda, moldes de tijolo, calibres, operações de brunimento, rolos e facas para corte de tiras. Os do grupo O, por fim, são utilizados em matrizes e punções para corte de chapas para estampagem, rebarbação, trefilação, flangeamento e forjamento.
· Aços resistentes ao choque: usados em talhadeiras, formões, contra-rebites, punções, brocas-guia e outras aplicações que requerem elevada tenacidade e resistência ao choque.
· Aços baixa-liga para aplicações especiais: são utilizados, de um modo geral, em componentes de máquinas como árvores, cames, placas, mandris e pinças de tornos
· Aços para moldagem: como o próprio nome sugere, estes aços são utilizados como moldes de vários tipos, para aplicações que requerem a manutenção das características de resistência em temperaturas e pressões elevadas.
· Aços temperáveis em água: são utilizados em ferramentas para forjamento a frio, cunhagem de moedas, gravação em relevo, trabalho em madeira, corte de metais duros (machos e alargadores), cutelaria e outras que requeiram resistência ao desgaste por abrasão.
COMO FABRICAR PASTILHAS DE METAL DURO
Fabricação do Pó
Os principais passos na preparação do pó de metal duro pronto para prensagem são:
- Pesagem do diferentes tipos de matéria-prima
- Mistura e moagem em proporções e tamanhos de grãos adequados - Secagem por spray para o pó acabado
- Identificação e estoque antes da prensagem
Os diferentes tipos de matéria-prima são entregues à fabrica. Dependendo da classe, são usados diferentes misturas e compostos. As principais matérias-primas normalmente são:
- Carboneto de Tungstênio (WC)
- Carboneto de Titânio e carboneto de Tungstênio (Ti,W)C
- Cobalto
- Carboneto de Tântalo e carboneto de Nióbio (Ta, Nb)C
- Polietilenoglicol (fase aglomeraste, cera)
O pó, nas proporções adequadas para a classe final, é transportado para a moagem. O pó é misturado com etanol e moído por horas até que o tamanho de grão específico seja obtido. A mistura é movida em um recipiente de coleta especial. A mistura do lote é então transportada para a secagem por spray.
Após a moagem, o líquido de moagem (etanol) deve ser separado do pó. Isso é feito bombeando-se a polpa para um funil para secagem por spray. O álcool é evaporado e se formam pequenos aglomerados que caem para o fundo. O pó misturado é passado através de um resfriado e coletado em containers.
O pó de metal duro acabado e pronto para prensagem é colocado em baldes, identificado e estocado. Aproximadamente 30 diferentes misturas de pó de metal duro são estocados, dependendo das proporções da classe com relação à resistência ao desgaste e tenacidade.
Prensagem
O método para manufaturar as ferramentas de prensagem é um complicado processo integrado aos sistemas CAD, onde as pastilhas são desenhadas para ferramentas de prensagem. Essas ferramentas consistem de uma matriz para prensagem, uma punção superior a outra inferior e um pino central para pastilhas com furo central.
A matriz é preenchida com pó de meta duro já misturado. O pó é prensado junto entre os punções superiores e inferiores. Com várias toneladas de pressão, as pastilhas são compactadas para respectiva geometria. Antes da sinterização, as pastilhas prensadas são muito sensíveis e macias com giz.
Antes da sinterização, as pastilhas prensadas possuem o dobro do tamanho de seu respectivo tamanho final. As pastilhas contraem 50% em volume e 20% em peso no processo de sinterização. As pastilhas prensadas são medidas em peso e altura. As trincas superficiais também são verificadas.
Sinterização
Os passos principais no processo de sinterização:
- As pastilhas prensadas são colocadas em pratos de grafite
- O processo de sinterização leva por volta de 12 horas com uma temperatura de aproximadamente 1500ºC
- Processamento de dados, controle ocular e medição
As pastilhas são colocadas em pratos de grafite. Dependendo da classe e do tamanho das pastilhas, os pratos são preparados para o seu respectivo processo de sinterização. A sinterização é um processo de tratamento térmico no qual fecham-se os poros, ocorrendo a cementação entre o aglomerante e os carbonetos(partículas duras), aumentando também a resistência.
Dependendo da classe, diferentes processos são desenvolvidos. Se a temperatura estiver desviando, diferentes tipos de passos de sintetização são usados, bem como fornecimento de diferentes gases e pressões, além de métodos de refrigeração. As pastilhas agora conseguiram grande tenacidade e resistência ao desgaste. As pastilhas contraíram-se para o seu respectivo tamanho final, ou seja aproximadamente 50% em volume.
O processo é estritamente controlado por um moderno sistema computadorizado. O menor desvio no processo dará um alarme aos operadores. É feito um controle ocular das pastilhas após o processo de sinterização. É feita também a medição de certos parâmetros antes das pastilhas deixarem o departamento de sinterização.
Retífica
Muitas pastilhas são retificadas ou lapidadas (desbastadas) em qualquer formato. As principais operações de retifica são:
- Lapidação na superfície superior e/ou inferior
- Retifica na periferia
- Retifica de chanfros e fases negativas
- Retifica de perfis (pastilhas para rosqueamento)
- Retifica de perfis/formatos especiais
Retífica completa das laterais, raios e chanfros são feitos em modernas máquinas de 5 eixos. Cada pastilha é fixada automaticamente e passa pela retifica o número de vezes igual ao número de chanfros a ser retificado. As dimensões são controladas por instrumentos especiais.
Modernos robôs manuseiam o fornecimento e carregamento de máquinas com pastilhas sem retífica acabadas para a fábrica. Após as operações de retífica, as pastilhas são transportadas para a próxima fase de produção: tratamento de aresta.
Tratamento da Aresta
O tratamento de aresta é realizado em quase todas as pastilhas. Através dessa operação, a aresta de corte é arredondada e reforçada. A vida útil da ferramenta depende fortemente do formato da aresta. Diferentes métodos vem sendo usados. O tamanho da parte arredondada da aresta é de aproximadamente 0.02 - 0.08 mm (0.007 - 0.003 polegadas).
Um método comum para o tratamento da aresta é o escovamento. Outros métodos são o jateamento seco e úmido da mesma. Dependendo do tipo, geometria, classe, raio de canto e tamanho da pastilha, o arredondamento da aresta e ajustado de acordo. As pastilhas para acabamento possuem um tratamento de aresta menor, comparado as pastilhas para desbaste.
Cobertura
As pastilhas de metal duro com cobertura são fabricadas colocando-se camadas sobre as mesmas, principalmente através do método de Deposição Química de Vapores (CVD - Chemical Vapour Deposition). Basicamente, a cobertura pelo processo CVD e feita através de reações químicas de diferentes gases. Outro método e a Deposição Física de Vapores (PVD - Physical Vapour Deposition) que é feita com uma temperatura de aproximadamente metade (500º C) daquela usada no CVD (1000º C).
Tanto a cobertura única quanto a multicamada são feitas através de processo químico com uma temperatura de aproximadamente 1000º C. Para ambos os tipos de cobertura várias substâncias, que reagem quimicamente umas com as outras para formar outros componentes, são injetadas dentro de um forno. As pastilhas a receberem a cobertura são colocadas dentro desse forno. Durante todo o ciclo de cobertura há uma subpressão no forno.
O processo leva aproximadamente de oito a dezesseis horas dependendo da classe. A espessura das coberturas em pastilhas intercambiáveis varia entre 2 a 12 microns (a média de um fio de cabelo tem um diâmetro de 58 microns). O carbonitreto de titânio e normalmente usado como primeira camada, Ti(CN). A cobertura de óxido de alumínio, AI2O3, também e geralmente usada. Uma camada fina de nitreto de titânio, TiN, na superfície da pastilha proporciona a cor dourada.
O processo de cobertura é rigorosamente controlado por um moderno sistema computadorizado. Durante o processo de cobertura, a quantidade de gás, a temperatura e a pressão, para controle da qualidade é de extrema importância. A combinação do substrato otimizado e o processo CVD/PVD desenvolvido resulta na atual geração de pastilhas de metal duro com cobertura para torneamento, fresamento e furação.
Gravação, Etiquetagem, Embalagem
Hoje, o controle ocular, gravação, etiquetagem e embalagem das pastilhas são feitos em maquinas completamente automatizadas. Robôs manuseiam as pastilhas, do carregamento nas maquinas até as prateleiras. O controle ocular do tamanho da pastilha, geometria e raio de canto também é feito por um sistema computadorizado, Códigos de barra são usados desde o inicio da fabricação das pastilhas até o estoque.
A classe e marcada a laser ao invés de marcação a tinta. As embalagens de pastilhas são etiquetadas e lacradas por robôs. A etiqueta com dados de corte CoroKey e adicionada por, último, na superfície das embalagens. Uma inspeção estatística final das pastilhas, através de microscópio e feita para avaliar dureza, trincas, tamanho do grão, dimensões, acabamento superficial e avarias.
Fonte: catálogo Sandvik 2008
Os principais passos na preparação do pó de metal duro pronto para prensagem são:
- Pesagem do diferentes tipos de matéria-prima
- Mistura e moagem em proporções e tamanhos de grãos adequados - Secagem por spray para o pó acabado
- Identificação e estoque antes da prensagem
Os diferentes tipos de matéria-prima são entregues à fabrica. Dependendo da classe, são usados diferentes misturas e compostos. As principais matérias-primas normalmente são:
- Carboneto de Tungstênio (WC)
- Carboneto de Titânio e carboneto de Tungstênio (Ti,W)C
- Cobalto
- Carboneto de Tântalo e carboneto de Nióbio (Ta, Nb)C
- Polietilenoglicol (fase aglomeraste, cera)
O pó, nas proporções adequadas para a classe final, é transportado para a moagem. O pó é misturado com etanol e moído por horas até que o tamanho de grão específico seja obtido. A mistura é movida em um recipiente de coleta especial. A mistura do lote é então transportada para a secagem por spray.
Após a moagem, o líquido de moagem (etanol) deve ser separado do pó. Isso é feito bombeando-se a polpa para um funil para secagem por spray. O álcool é evaporado e se formam pequenos aglomerados que caem para o fundo. O pó misturado é passado através de um resfriado e coletado em containers.
O pó de metal duro acabado e pronto para prensagem é colocado em baldes, identificado e estocado. Aproximadamente 30 diferentes misturas de pó de metal duro são estocados, dependendo das proporções da classe com relação à resistência ao desgaste e tenacidade.
Prensagem
O método para manufaturar as ferramentas de prensagem é um complicado processo integrado aos sistemas CAD, onde as pastilhas são desenhadas para ferramentas de prensagem. Essas ferramentas consistem de uma matriz para prensagem, uma punção superior a outra inferior e um pino central para pastilhas com furo central.
A matriz é preenchida com pó de meta duro já misturado. O pó é prensado junto entre os punções superiores e inferiores. Com várias toneladas de pressão, as pastilhas são compactadas para respectiva geometria. Antes da sinterização, as pastilhas prensadas são muito sensíveis e macias com giz.
Antes da sinterização, as pastilhas prensadas possuem o dobro do tamanho de seu respectivo tamanho final. As pastilhas contraem 50% em volume e 20% em peso no processo de sinterização. As pastilhas prensadas são medidas em peso e altura. As trincas superficiais também são verificadas.
Sinterização
Os passos principais no processo de sinterização:
- As pastilhas prensadas são colocadas em pratos de grafite
- O processo de sinterização leva por volta de 12 horas com uma temperatura de aproximadamente 1500ºC
- Processamento de dados, controle ocular e medição
As pastilhas são colocadas em pratos de grafite. Dependendo da classe e do tamanho das pastilhas, os pratos são preparados para o seu respectivo processo de sinterização. A sinterização é um processo de tratamento térmico no qual fecham-se os poros, ocorrendo a cementação entre o aglomerante e os carbonetos(partículas duras), aumentando também a resistência.
Dependendo da classe, diferentes processos são desenvolvidos. Se a temperatura estiver desviando, diferentes tipos de passos de sintetização são usados, bem como fornecimento de diferentes gases e pressões, além de métodos de refrigeração. As pastilhas agora conseguiram grande tenacidade e resistência ao desgaste. As pastilhas contraíram-se para o seu respectivo tamanho final, ou seja aproximadamente 50% em volume.
O processo é estritamente controlado por um moderno sistema computadorizado. O menor desvio no processo dará um alarme aos operadores. É feito um controle ocular das pastilhas após o processo de sinterização. É feita também a medição de certos parâmetros antes das pastilhas deixarem o departamento de sinterização.
Retífica
Muitas pastilhas são retificadas ou lapidadas (desbastadas) em qualquer formato. As principais operações de retifica são:
- Lapidação na superfície superior e/ou inferior
- Retifica na periferia
- Retifica de chanfros e fases negativas
- Retifica de perfis (pastilhas para rosqueamento)
- Retifica de perfis/formatos especiais
Retífica completa das laterais, raios e chanfros são feitos em modernas máquinas de 5 eixos. Cada pastilha é fixada automaticamente e passa pela retifica o número de vezes igual ao número de chanfros a ser retificado. As dimensões são controladas por instrumentos especiais.
Modernos robôs manuseiam o fornecimento e carregamento de máquinas com pastilhas sem retífica acabadas para a fábrica. Após as operações de retífica, as pastilhas são transportadas para a próxima fase de produção: tratamento de aresta.
Tratamento da Aresta
O tratamento de aresta é realizado em quase todas as pastilhas. Através dessa operação, a aresta de corte é arredondada e reforçada. A vida útil da ferramenta depende fortemente do formato da aresta. Diferentes métodos vem sendo usados. O tamanho da parte arredondada da aresta é de aproximadamente 0.02 - 0.08 mm (0.007 - 0.003 polegadas).
Um método comum para o tratamento da aresta é o escovamento. Outros métodos são o jateamento seco e úmido da mesma. Dependendo do tipo, geometria, classe, raio de canto e tamanho da pastilha, o arredondamento da aresta e ajustado de acordo. As pastilhas para acabamento possuem um tratamento de aresta menor, comparado as pastilhas para desbaste.
Cobertura
As pastilhas de metal duro com cobertura são fabricadas colocando-se camadas sobre as mesmas, principalmente através do método de Deposição Química de Vapores (CVD - Chemical Vapour Deposition). Basicamente, a cobertura pelo processo CVD e feita através de reações químicas de diferentes gases. Outro método e a Deposição Física de Vapores (PVD - Physical Vapour Deposition) que é feita com uma temperatura de aproximadamente metade (500º C) daquela usada no CVD (1000º C).
Tanto a cobertura única quanto a multicamada são feitas através de processo químico com uma temperatura de aproximadamente 1000º C. Para ambos os tipos de cobertura várias substâncias, que reagem quimicamente umas com as outras para formar outros componentes, são injetadas dentro de um forno. As pastilhas a receberem a cobertura são colocadas dentro desse forno. Durante todo o ciclo de cobertura há uma subpressão no forno.
O processo leva aproximadamente de oito a dezesseis horas dependendo da classe. A espessura das coberturas em pastilhas intercambiáveis varia entre 2 a 12 microns (a média de um fio de cabelo tem um diâmetro de 58 microns). O carbonitreto de titânio e normalmente usado como primeira camada, Ti(CN). A cobertura de óxido de alumínio, AI2O3, também e geralmente usada. Uma camada fina de nitreto de titânio, TiN, na superfície da pastilha proporciona a cor dourada.
O processo de cobertura é rigorosamente controlado por um moderno sistema computadorizado. Durante o processo de cobertura, a quantidade de gás, a temperatura e a pressão, para controle da qualidade é de extrema importância. A combinação do substrato otimizado e o processo CVD/PVD desenvolvido resulta na atual geração de pastilhas de metal duro com cobertura para torneamento, fresamento e furação.
Gravação, Etiquetagem, Embalagem
Hoje, o controle ocular, gravação, etiquetagem e embalagem das pastilhas são feitos em maquinas completamente automatizadas. Robôs manuseiam as pastilhas, do carregamento nas maquinas até as prateleiras. O controle ocular do tamanho da pastilha, geometria e raio de canto também é feito por um sistema computadorizado, Códigos de barra são usados desde o inicio da fabricação das pastilhas até o estoque.
A classe e marcada a laser ao invés de marcação a tinta. As embalagens de pastilhas são etiquetadas e lacradas por robôs. A etiqueta com dados de corte CoroKey e adicionada por, último, na superfície das embalagens. Uma inspeção estatística final das pastilhas, através de microscópio e feita para avaliar dureza, trincas, tamanho do grão, dimensões, acabamento superficial e avarias.
Fonte: catálogo Sandvik 2008
DESGASTE E AVARIAS EM PASTILHAS INTERCAMBIÁVEIS
DESGASTE FRONTAL
Causas:
Velocidade de corte elevada
Pastilha muito tenaz
Soluções:
Reduzir a velocidade de corte
Empregar uma classe mais resistente ao desgaste
LASCAMENTO
Causas:
Aresta de corte frágil
Vibrações
Classe muito dura
Soluções:
Melhorar a estabilidade da ferramenta
Empregar uma classe mais tenaz
Empregar uma pastilha com aresta mais resistente
ARESTA POSTIÇA
Causas:
Velocidade de corte baixa
Materiais tenazes
Soluções:
Aumentar a velocidade de corte
Escolher uma geometria mais positiva
CRATERIZAÇÃO
Causas:
Velocidade de corte elevada
Avanço alto
Soluções:
Reduzir a velocidade de corte
Diminuir o avanço
Empregar uma classe mais resistente a formação de crateras
DEFORMAÇÃO PLÁSTICA
Causas:
Altos avanços
Grandes esforços de corte
Temperatura de corte muito elevada
Soluções:
Reduzir a velocidade de corte
Reduzir o avanço
Empregar uma pastilha mais resistente a deformação
Causas:
Velocidade de corte elevada
Pastilha muito tenaz
Soluções:
Reduzir a velocidade de corte
Empregar uma classe mais resistente ao desgaste
LASCAMENTO
Causas:
Aresta de corte frágil
Vibrações
Classe muito dura
Soluções:
Melhorar a estabilidade da ferramenta
Empregar uma classe mais tenaz
Empregar uma pastilha com aresta mais resistente
ARESTA POSTIÇA
Causas:
Velocidade de corte baixa
Materiais tenazes
Soluções:
Aumentar a velocidade de corte
Escolher uma geometria mais positiva
CRATERIZAÇÃO
Causas:
Velocidade de corte elevada
Avanço alto
Soluções:
Reduzir a velocidade de corte
Diminuir o avanço
Empregar uma classe mais resistente a formação de crateras
DEFORMAÇÃO PLÁSTICA
Causas:
Altos avanços
Grandes esforços de corte
Temperatura de corte muito elevada
Soluções:
Reduzir a velocidade de corte
Reduzir o avanço
Empregar uma pastilha mais resistente a deformação
domingo, 4 de outubro de 2009
Temperatura de corte no torneamento
Os valores das proporções variam com:
• o material da ferramenta e da peça;
• a forma da ferramenta;
• as condições de usinagem.
A temperatura da ferramenta se elevará de acordo com o calor específico e a condutibilidade térmica dos corpos em contato, além das dimensões das seções onde se escoa o calor.
A temperatura é o principal fator limitante da utilização das ferramentas de corte em regimes de trabalho elevados, fixando, portanto as condições máximas de produtividade e duração das ferramentas.
Como as deformações e forças de atrito se distribuem irregularmente, o calor produzido também se distribui de forma irregular.
A quantidade de calor devida ao atrito do cavaco com a superfície de saída e que vai à ferramenta, é relativamente pequena. Porém, como esta superfície de contato é reduzida, desenvolvem-se ali temperaturas significantes.
A quantidade de calor gerada aumenta com a velocidade e com a força de corte. Conseqüentemente, a temperatura cresce com o aumento da velocidade de corte, do avanço e da profundidade.
Este aumento de temperatura é acelerado com o desgaste da ferramenta, o qual aumenta o valor do coeficiente de atrito e conseqüentemente a força de corte.
Para aumentar a produtividade da ferramenta deve-se aumentar a velocidade, o avanço e a profundidade de corte. Todos estes fatores aumentam a temperatura. Portanto deve-se procurar diminuir esta temperatura além de empregar materiais de corte resistentes a altas temperaturas e ao desgaste.
O meio mais barato para a diminuição da temperatura de corte é o emprego de fluidos de corte.
• o material da ferramenta e da peça;
• a forma da ferramenta;
• as condições de usinagem.
A temperatura da ferramenta se elevará de acordo com o calor específico e a condutibilidade térmica dos corpos em contato, além das dimensões das seções onde se escoa o calor.
A temperatura é o principal fator limitante da utilização das ferramentas de corte em regimes de trabalho elevados, fixando, portanto as condições máximas de produtividade e duração das ferramentas.
Como as deformações e forças de atrito se distribuem irregularmente, o calor produzido também se distribui de forma irregular.
A quantidade de calor devida ao atrito do cavaco com a superfície de saída e que vai à ferramenta, é relativamente pequena. Porém, como esta superfície de contato é reduzida, desenvolvem-se ali temperaturas significantes.
A quantidade de calor gerada aumenta com a velocidade e com a força de corte. Conseqüentemente, a temperatura cresce com o aumento da velocidade de corte, do avanço e da profundidade.
Este aumento de temperatura é acelerado com o desgaste da ferramenta, o qual aumenta o valor do coeficiente de atrito e conseqüentemente a força de corte.
Para aumentar a produtividade da ferramenta deve-se aumentar a velocidade, o avanço e a profundidade de corte. Todos estes fatores aumentam a temperatura. Portanto deve-se procurar diminuir esta temperatura além de empregar materiais de corte resistentes a altas temperaturas e ao desgaste.
O meio mais barato para a diminuição da temperatura de corte é o emprego de fluidos de corte.
quarta-feira, 30 de setembro de 2009
Propriedades dos materiais
A)Propriedades Físicas:
1. Condutibilidade térmica:
Propriedade que os corpos possuem em conduzir mais rápido a corrente térmica (frio ou calor).
2. Condutibilidade elétrica:
É a facilidade que os corpos tem em permitir ou não a propagação da corrente elétrica.
3. Ponto de fusão:
Temperatura na qual um corpo adquire a propriedade da fusibilidade
4. Resistência:
Carga máxima que um material pode resistir sem se deformar, através de tração, torção, flexão e cisalhamento.
5. Dureza:
Capacidade de um material de se opor à penetração de um outro corpo.
6. Elasticidade:
Capacidade que um corpo possui, ao ser deformado, e quando cessados os esforços, retornar a sua forma original.
7. Plasticidade:
Capacidade que um corpo possui, ao ser deformado, e quando cessados os esforços, não retornar a sua forma original.
8. Peso:
É a massa do elemento ( em g) multiplicada pela gravidade (em m/s2).
9. Dilatação térmica:
Ao aumentar a temperatura os corpos se dilatam (aumentam seu volume), em todas as direções.
10. Magnetismo:
Capacidade que os corpos possuem em serem atraídos ou repelidos por um imã.
B)Propriedades Químicas:
1. Corrosibilidade:
É a resist6encia que os corpos oferecem ao ataque pelo meio ambiente ( corrosão), ou pelo efeito da temperatura ( oxidação).
2. Combustibilidade:
É o processo químico, em que existe a combinação do elemento com o O, liberando luz e calor.
3. Toxibilidade (toxidez):
Efeito dos elementos em serem prejudiciais ao ser humano.
4. Valência:
Capacidade de os átomos unirem-se em moléculas, com base na força de coesão. A combinação de um átomo de H com outro elemento é chamada monovalente, se dois átomos combinarem-se com o elemento é bivalente, a valência indica com quantos átomos de H um elemento pode unir-se ou substituir.
5. Afinidade:
Afinidade: é a força de atração entre os átomos.
C) Propriedades tecnológicas:
1. Fusibilidade:
Capacidade dos corpos em sofrerem fusão.
2. Soldabilidade:
Propriedade dos materiais em unirem-se através de fusão ou pressão.
3. Forjabilidade:
Capacidade dos corpos em terem sua forma alterada por golpes e calor.
4. Usinabilidade:
São mecanismos de corte ou arranque de cavacos, onde é aplicada uma força sobre o material, para que se rompam as partículas.
1. Condutibilidade térmica:
Propriedade que os corpos possuem em conduzir mais rápido a corrente térmica (frio ou calor).
2. Condutibilidade elétrica:
É a facilidade que os corpos tem em permitir ou não a propagação da corrente elétrica.
3. Ponto de fusão:
Temperatura na qual um corpo adquire a propriedade da fusibilidade
4. Resistência:
Carga máxima que um material pode resistir sem se deformar, através de tração, torção, flexão e cisalhamento.
5. Dureza:
Capacidade de um material de se opor à penetração de um outro corpo.
6. Elasticidade:
Capacidade que um corpo possui, ao ser deformado, e quando cessados os esforços, retornar a sua forma original.
7. Plasticidade:
Capacidade que um corpo possui, ao ser deformado, e quando cessados os esforços, não retornar a sua forma original.
8. Peso:
É a massa do elemento ( em g) multiplicada pela gravidade (em m/s2).
9. Dilatação térmica:
Ao aumentar a temperatura os corpos se dilatam (aumentam seu volume), em todas as direções.
10. Magnetismo:
Capacidade que os corpos possuem em serem atraídos ou repelidos por um imã.
B)Propriedades Químicas:
1. Corrosibilidade:
É a resist6encia que os corpos oferecem ao ataque pelo meio ambiente ( corrosão), ou pelo efeito da temperatura ( oxidação).
2. Combustibilidade:
É o processo químico, em que existe a combinação do elemento com o O, liberando luz e calor.
3. Toxibilidade (toxidez):
Efeito dos elementos em serem prejudiciais ao ser humano.
4. Valência:
Capacidade de os átomos unirem-se em moléculas, com base na força de coesão. A combinação de um átomo de H com outro elemento é chamada monovalente, se dois átomos combinarem-se com o elemento é bivalente, a valência indica com quantos átomos de H um elemento pode unir-se ou substituir.
5. Afinidade:
Afinidade: é a força de atração entre os átomos.
C) Propriedades tecnológicas:
1. Fusibilidade:
Capacidade dos corpos em sofrerem fusão.
2. Soldabilidade:
Propriedade dos materiais em unirem-se através de fusão ou pressão.
3. Forjabilidade:
Capacidade dos corpos em terem sua forma alterada por golpes e calor.
4. Usinabilidade:
São mecanismos de corte ou arranque de cavacos, onde é aplicada uma força sobre o material, para que se rompam as partículas.
Assinar:
Postagens (Atom)
links interessantes
Giuberto Kanzler
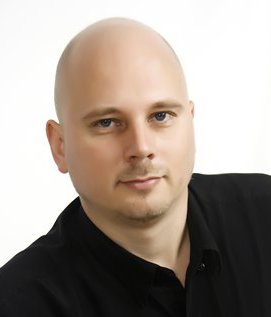
Engenheiro de Produção